At DWG, we write masses of articles. Blogs about the latest technologies and systems, stories contributed by/about DWG colleagues, and the occasional opinion piece. So what do we hope to achieve? We want to inform you: ‘Well I’ll be, so that’s how it works?!’. A previous poll identified a clear winning topic: integrated engineering. The result? That’s this blog, enjoy the read!
Inventions that have an impact
Why do things the hard way? This might even be one of the oldest sayings in the world. Our need for convenience has led to continuous advances in human society. From rolling logs to the wheel, from the horse to engines, from wheeled transport and ships to aircraft.
Ultimately, these impactful inventions have resulted in the IT-permeated world we live in today. Can you remember the very early days, when PCs were actually glorified word processors? Nowadays, all systems are interconnected and devices are making each other (and humans) smarter and smarter.
From faxes to system integration
I am old enough to remember a time when, as an internal sales representative, I had to manually enter orders in the sales system so that the sales manager could report on monthly sales. That was back in the late 1990s. Then I printed a copy of the information in the system, stapled the customer order to it and walked over to the administration department where I handed it in. That department had its own system for entering purchases. Of course, everything was printed out and put in large lever arch files so that the orders could always be found.
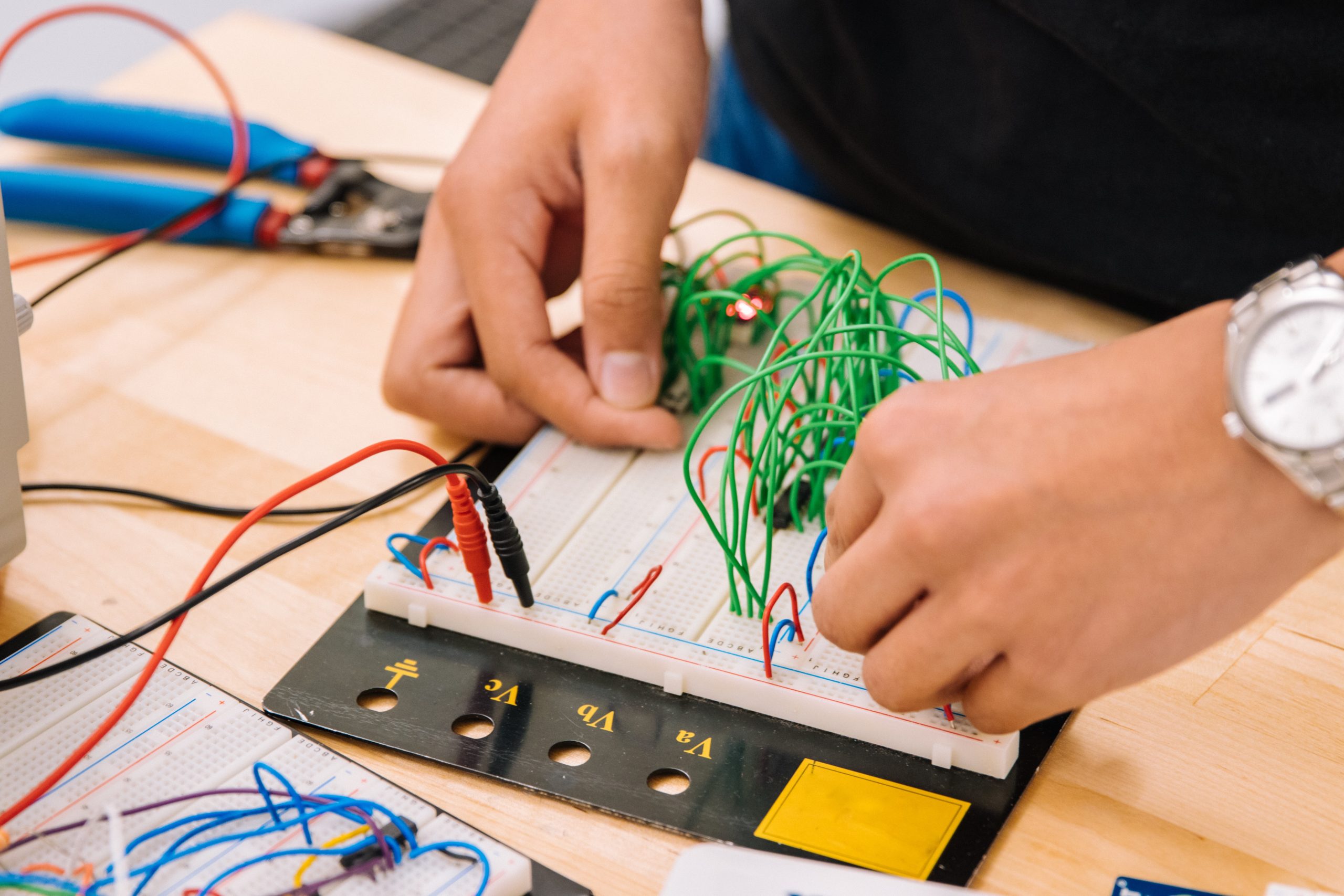
Fun fact: orders came in on the fax machine or by post. Companies that did not have a fax ordered on the phone. Pretty labour-intensive when you think about it. Fortunately, the integration of all these systems has resulted in significant time savings.
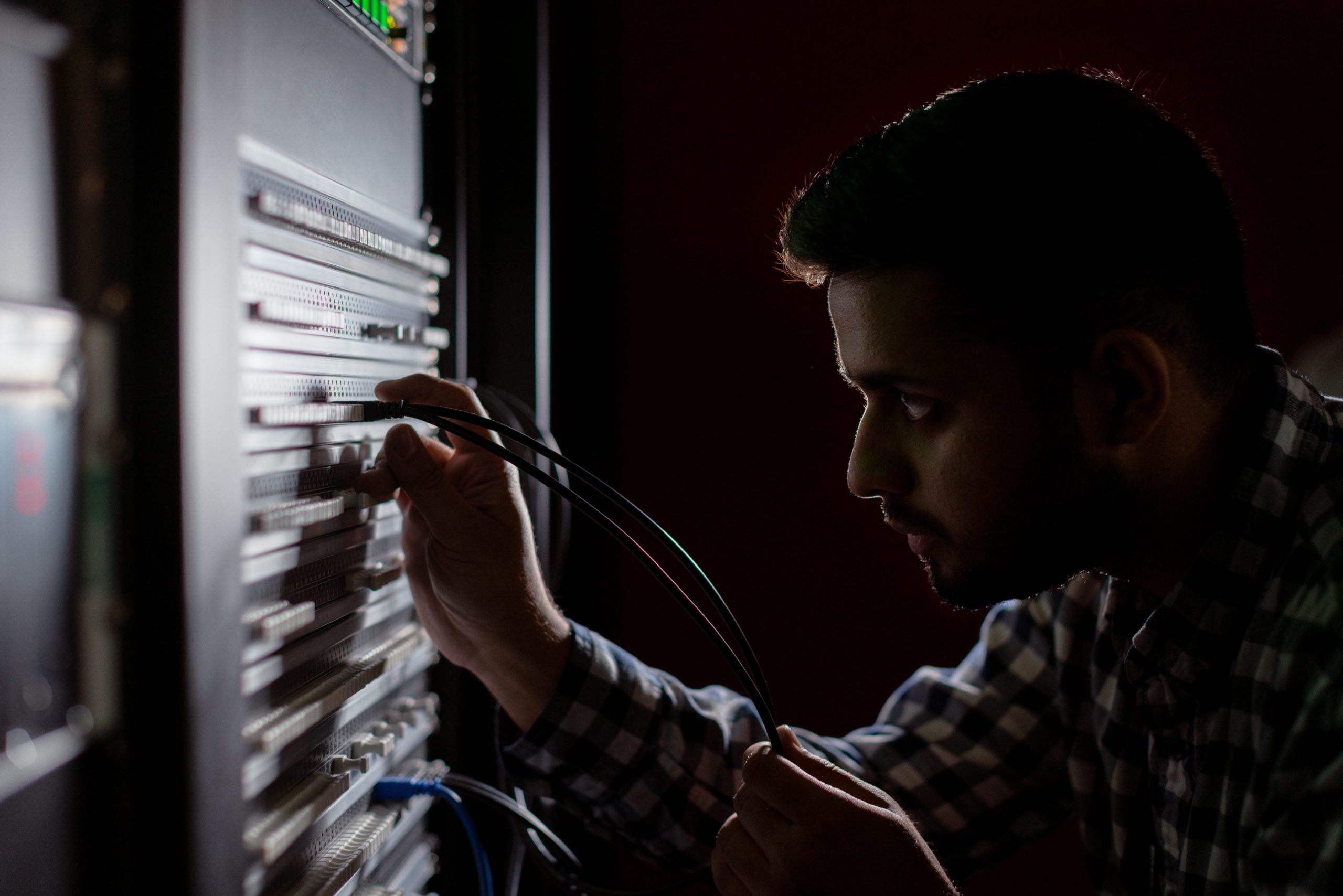
How does system integration work in industry?
How do those benefits translate to industry? Traditionally, industry always lags slightly behind office automation. One reason for this is that the installations are used in production around the clock. After all, downtime is very costly.
PLCs and HMI screens were an effective replacement for relay control systems. Until the DCS system was introduced in the 1970s. This was the first system to fully integrate the operator controls and system controls in a configuration based on standard function blocks.
These systems were immediately adopted by the oil and gas industry. However for the food and manufacturing industries, the DCS system was still a bridge too far. Fortunately, further systems such as the PCS7 from Siemens came on the market in the 1990s. These developments have resulted in other industries moving to integrated engineering as well.
Integrated engineering in industrial automation
In today’s environment, it is actually quite common to apply integrated engineering to less complex industrial automation issues. For example, Siemens launched another important advance a few years ago when it introduced the TIA Portal and the new S7-1200 and S7-1500 PLCs.
All major automation components are integrated in TIA Portal and everything can be programmed. For example, everything from controllers and drives to HMI, safety, motion control, peripheral equipment and even energy management. A consistent database and libraries of commonly used functions make the engineering work faster and easier. Several people can access a project at the same time. In addition, synchronisation occurs automatically and tasks – both device-oriented and task-oriented – can be flexibly processed and performed simultaneously. Engineering in the cloud is also included in this solution. Many more developments are almost certainly on the way in the next few years.
The level of software integration between disciplines has also advanced considerably. More and more companies are discovering the benefits of an integrated system. In systems like these, process, software and hardware engineers can work together to produce a joint result. This is because a change in a P&ID is automatically reflected in the software and vice versa.