Opinion piece on intensive process technology. Enrico, a colleague at DWG, is genuinely concerned about our position in relation to the chemical industry in Europe. He believes that we need to adopt a new strategy. A strategy that is committed to minimising the use of energy and raw materials needed to make products. In this article, Enrico talks about the innovative technologies needed to turn the tide.
The infrastructure in the Netherlands
“It is probably true to say that the Netherlands has a slight lead over other countries because of its excellent infrastructure of (deep) waterways, extensive rail and road networks and integrated business operations. But if we continue in the same way as before, we will soon lose this position. The underlying factors are not only the lower labour costs and cheaper energy in distant countries; the questionable interpretation of European environmental legislation in the Netherlands is a further risk.
So that is not an area where we can win anything. Indeed, as our own gas supplies become increasingly depleted, making us more and more dependent on Russia, we will have no option but to change course. Particularly in the light of the huge projected reserves of shale oil and shale gas in the United States. We must adopt a strategy that is committed to minimising the use of energy and raw materials needed to make our products. This will require innovative technologies that make the processes many times more effective and efficient than they have been to date.”
What are the ideal circumstances?
“Fortunately, those technologies already exist. In the world of process technology, this transition is called process intensification (PI). The philosophy of process intensification has traditionally been characterised as: smaller, cheaper and safer. It is defined as the development of new equipment and technologies that are expected to bring substantial improvements in production processes and lead to substantial equipment downsizing. The result is substantially lower energy and resource consumption and less production of waste (Stankiewicz & Moulin, 2000).
Reducing the size of the equipment and/or combining both a chemical reaction and a chemical separation in an item of equipment, results in a near perfect approximation of the ideal circumstances for a chemical or physical process. A membrane reactor is a good example: the molecules are first separated by the membrane, and are then very efficiently introduced into a chemical reaction there in the reactor.”
Is process intensification a common phenomenon across the chemical industry?
“Well, surprisingly it isn’t … The chemical industry in the Netherlands consumes about 500 PJ of energy each year: a colossal amount that you can’t even visualise (500 followed by 15 zeros, equating to 500 trillion or 500 million billion joules).
Distillation accounts for about 40% of that figure. Assume for a moment (conservatively) that a dividing wall column can achieve an energy saving of 20%, and that the installation can be applied to 33% of all columns. That would give us a potential saving of 13 PJ. This is roughly equivalent to the annual energy consumption of 500,000 households! As far as we know, this column has not been used in bulk chemical industry applications in the Netherlands and certainly not on this scale. It’s hardly surprising then that a German university chose a slightly mysterious title for its presentation on this subject: ‘Dividing wall columns – which wall separates Dutch industry from application?’ If you know the answer, please tell us…”
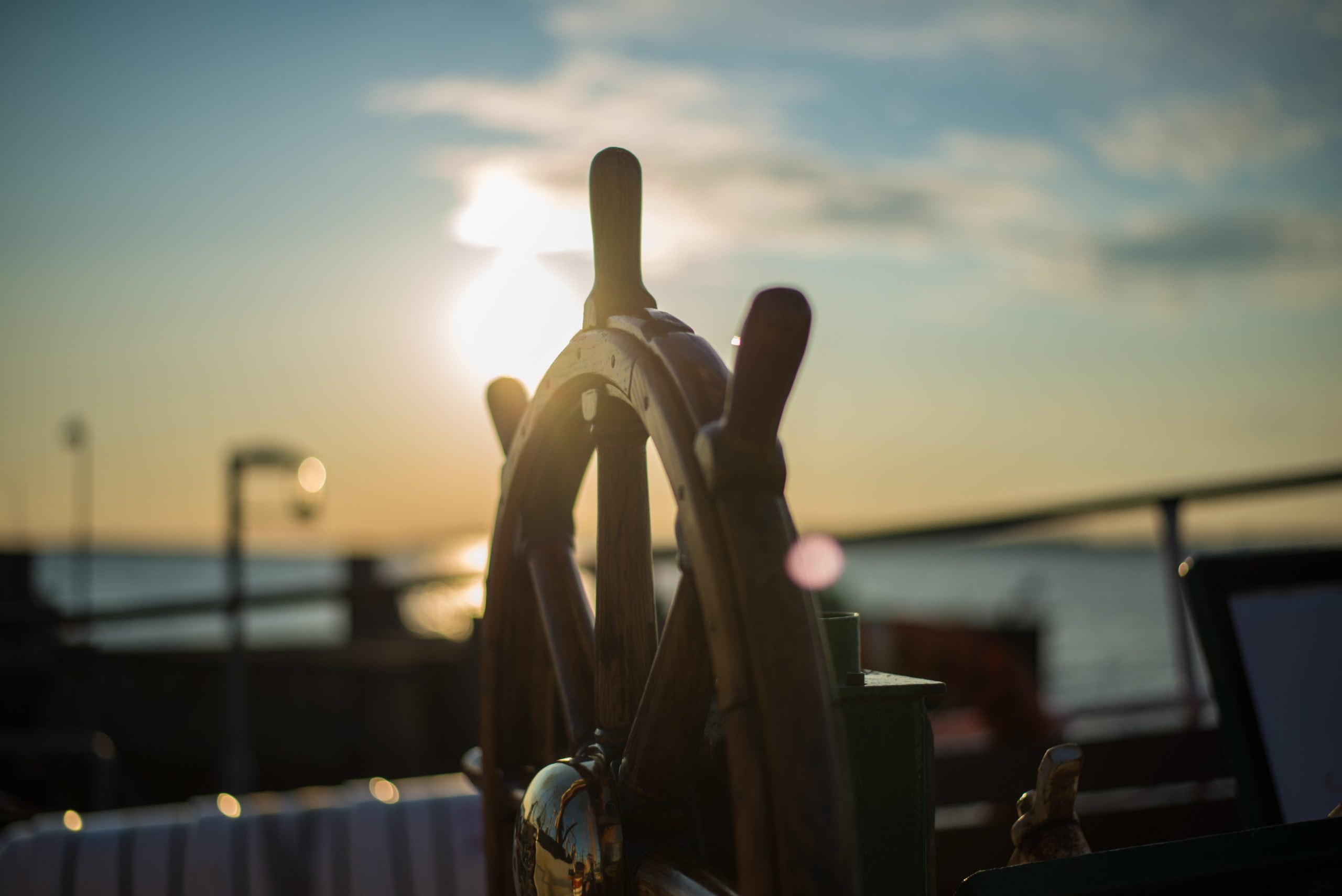
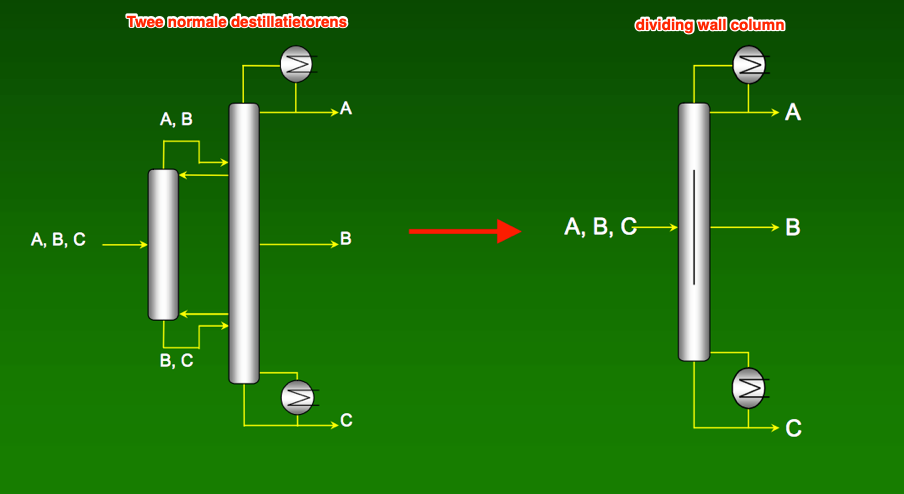
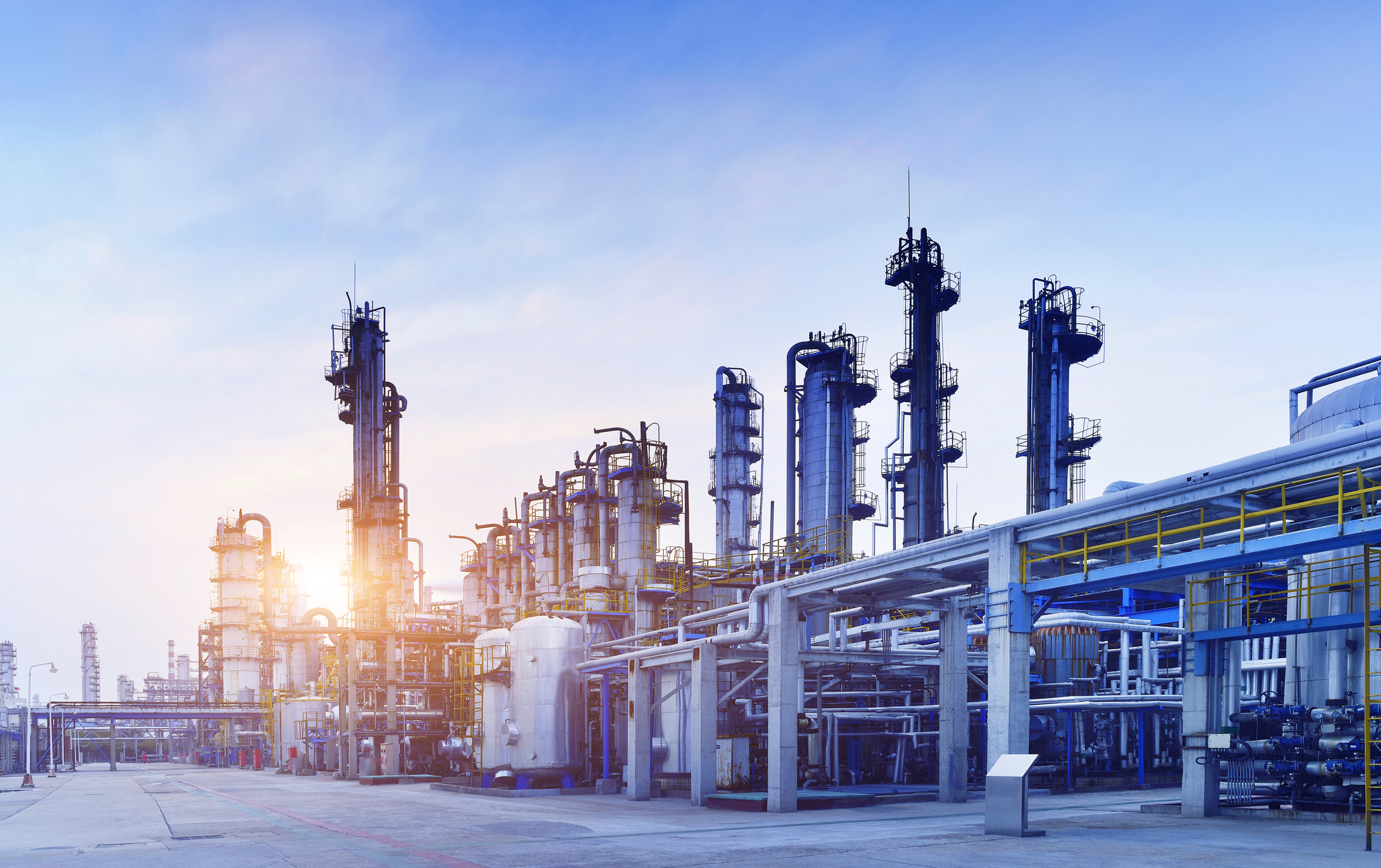